板式喂料机自动喂料控制改造与应用
原料配料站设备是由计量皮带秤和板式喂料机组成,皮带秤和板式喂料机均为变频调速控制,原设计由板式喂料机给计量皮带秤供应原料,由下料管直接下料到皮带秤机尾,下料管内可存放约2吨物料,皮带秤是由积算仪进行控制,设定皮带秤的给定量,皮带秤积算仪根据实际流量反馈进行自动调节秤速度,跟随给定量。板式喂料机由程序上的PID功能块进行控制的,根据皮带秤的给定、反馈来调节板式喂料机的速度,调整给料。
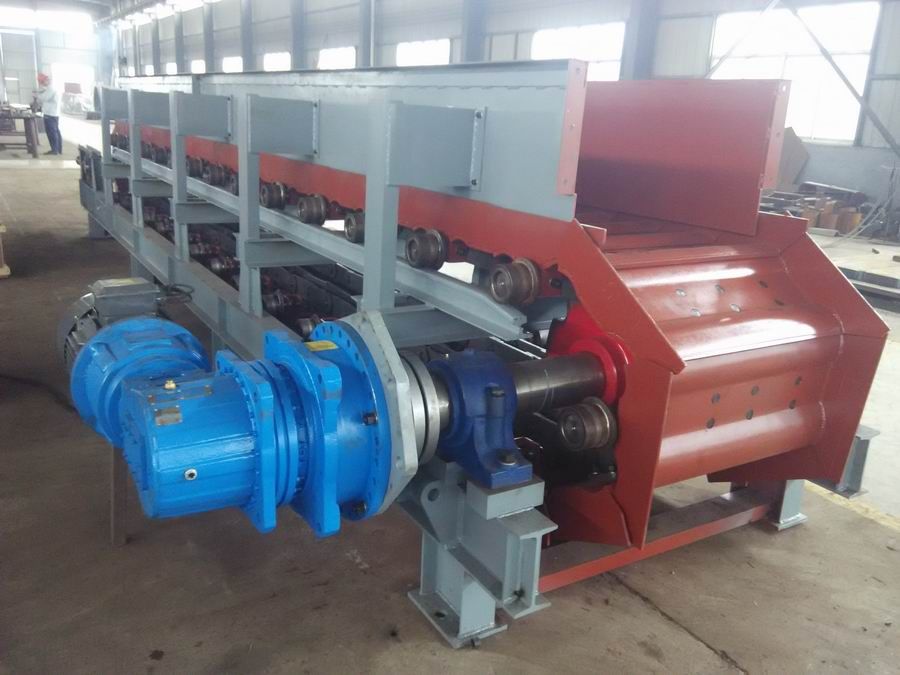
一、在实际运行中存在的问题:
1、由于两台设备中间有约2吨的缓冲,皮带秤反馈不是板式喂料机的直接变量,这样控制会出现空料或溢料情况发生,空料造成配料波动,影响产品质量,溢料造成职工增加甚至损坏设备。
2、由于配料比例的变化,当配料比例较小时,板式喂料机的低速度输送量已经超过物料配料使用量,所以没有调速,只能通过启停板式喂料机来供应物料。实际运行中,需要现场人员观察并频繁的手动启停设备。
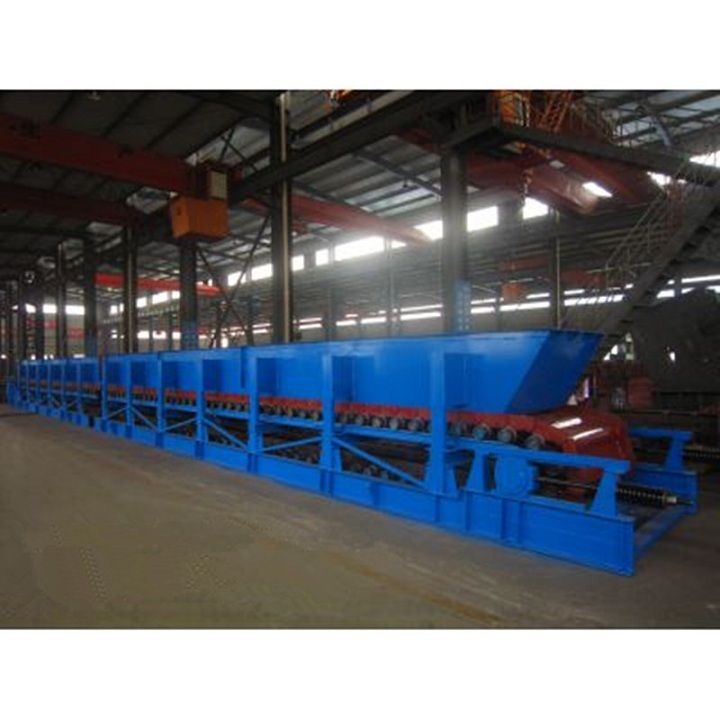
二、原因分析:
1、皮带秤称重信号不是板式喂料机的直接变量,作为板喂机调速参数设置不合理。
2、板式喂料机的输送能力过大,与配料比例较低用料量不匹配。
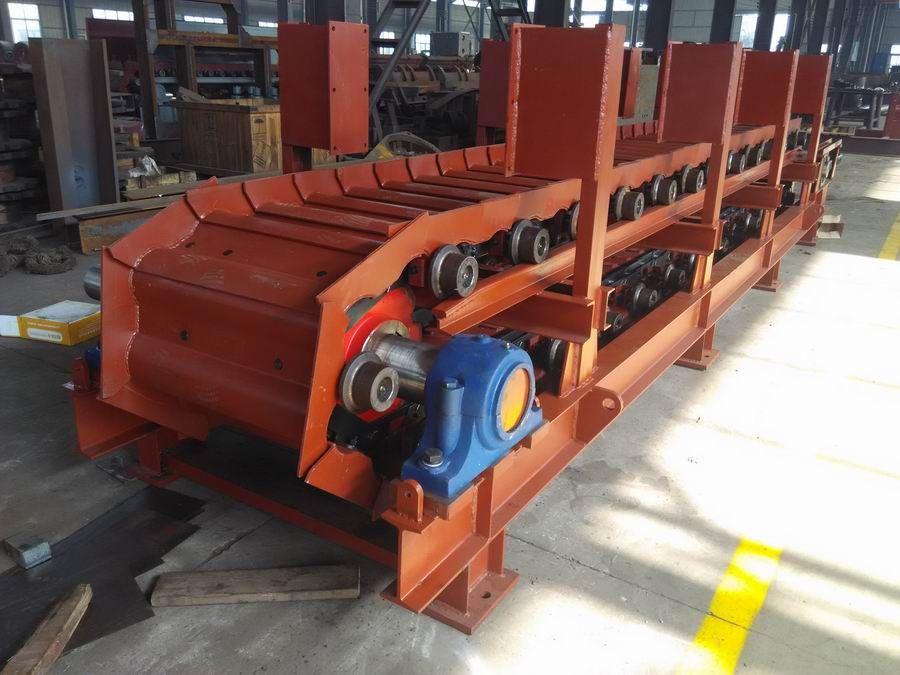
三、提出解决思路,确定解决办法:
思路1:在皮带秤机尾部,板式喂料机的下料管下方位置安装一组计量托辊,用来计量下料管内的物料重量,以此重量反馈给PID功能块,来控制板式喂料机的速度,保持下料管里的物料始终在一个合理范围内。同时在程序上设置重量的上下限,确保不断料、不溢料。保证给皮带秤的供料充足稳定。
思路2:在料管的高低位安装上下料位开关,以此信号来控制开停机。
思路3:用料位计进行测量,将料位的高低值以模拟量信号送给PLC模块,再由程序做判断,控制开停机。
现场测试:在实际测试中,由于料管截面积较小,下料时几乎占据了所有料管,导致下限位开关被冲击和冲刷,严重影响准确度和寿命,难以保证正常使用。而料位计正常情况下不能安装在下料口,所以也不能作为测量信号。测试中还发现下料管内的物料多少与计量称重重量并非线性关系,在重量低于1吨时线性关系较好,重量超过1吨时误差较大,通过重量反馈实现PID功能调节难以满足当前的控制需求。所以,考虑用重量的下限作为启动板式喂料机的信号,并在下料管的上限位安装料位开关,以此信号作为停止板式喂料机的信号。
确定解决办法:根据现场实际测试结果,确定了相对比较理想的办法,即采用称重计量信号作为下限信号,上限信号用料位开关来实现设备的启动停止,同时利用新的重量信号作为反馈引入到原PID功能块的反馈引脚,在用料量大时可实现自动调速控制。
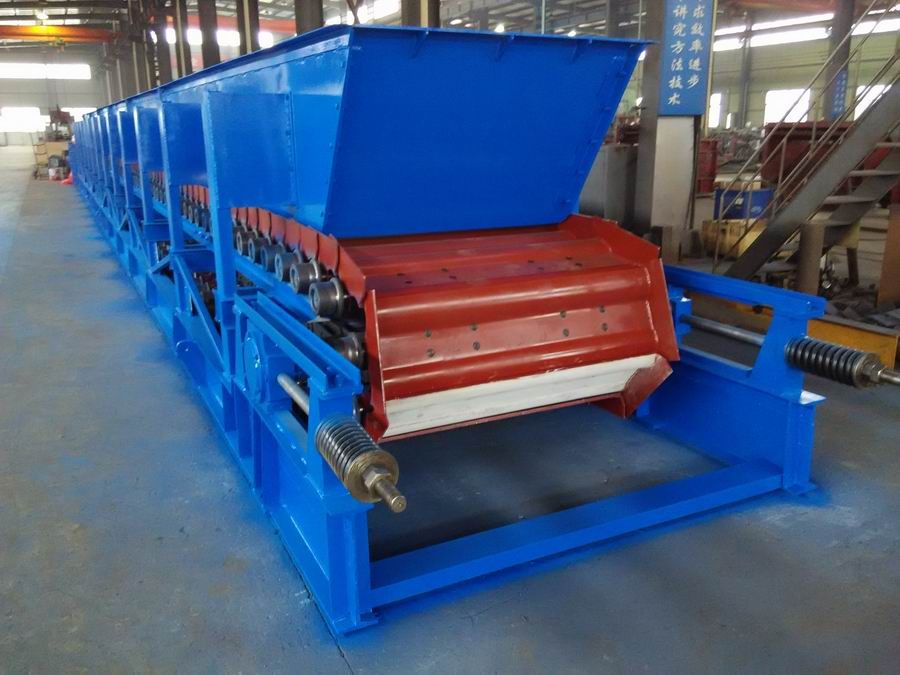
四、改造过程:
1、现场改造:将称重传感器通过接线盒汇总后接入称重仪表,称重仪表把重量信号以4-20ma信号经过信号隔离器送入PLC的模拟量输入模块。在下料斗的物料上限位置安装一个阻旋式料位开关,并将开关量信号接入PLC的开关量模块。
2、控制逻辑:
(1)、在组启动信号到来时,用称重重量与设定重量进行比较,小于设定重量则启动板式喂料机,当有上限位信号时,将信号与急停信号并联,这样就实现了自动启停。
(2)、用新的重量信号代替原称重信号,引入到原PID程序块的的重量反馈引脚,可实现用量比例较大时的自动调速控制,将物料重量稳定在设定值附近。
五、改造效果:改造后完全实现了自动控制,解决了空料、溢料、配料波动造成的产品质量问题,经过三个月的使用,工作稳定可靠,不仅满足了工艺的要求,还缓解了现场作业人员的工作压力。
电话:13606279786
板喂机46
板式喂料机45
板式喂料机44
板式喂料机40
以上是板式喂料机自动喂料控制改造与应用的详细介绍,包括板式喂料机自动喂料控制改造与应用的厂家、价格、型号、图片、产地、品牌等信息!